Why Does Concrete Cure, Not Dry?
Concrete is everywhere. From sidewalks and parking garages to bridges and stadiums, it’s one of the most widely used construction materials in the world. But there’s one big misconception many people have about it: that concrete “dries” to become hard.
In reality, concrete doesn’t dry. It cures. And understanding the difference is essential for building structures that are safe, strong, and built to last.
What’s the Difference Between Drying and Curing?
When most materials harden, they do so by drying. Paint dries as its liquid evaporates. Glue hardens when its moisture content is gone.
Concrete, on the other hand, hardens through a chemical process called hydration. Water reacts with cement to form calcium-silicate-hydrate (C-S-H), the compound that gives concrete its strength.
This reaction requires moisture to stay present inside the concrete for several days after placement. If the water evaporates too early, the concrete will not fully hydrate, and that leads to long-term problems.
According to the American Concrete Institute (ACI 308R-01), curing is the process of maintaining moisture and temperature conditions in freshly placed concrete to allow for proper hydration of the cement.
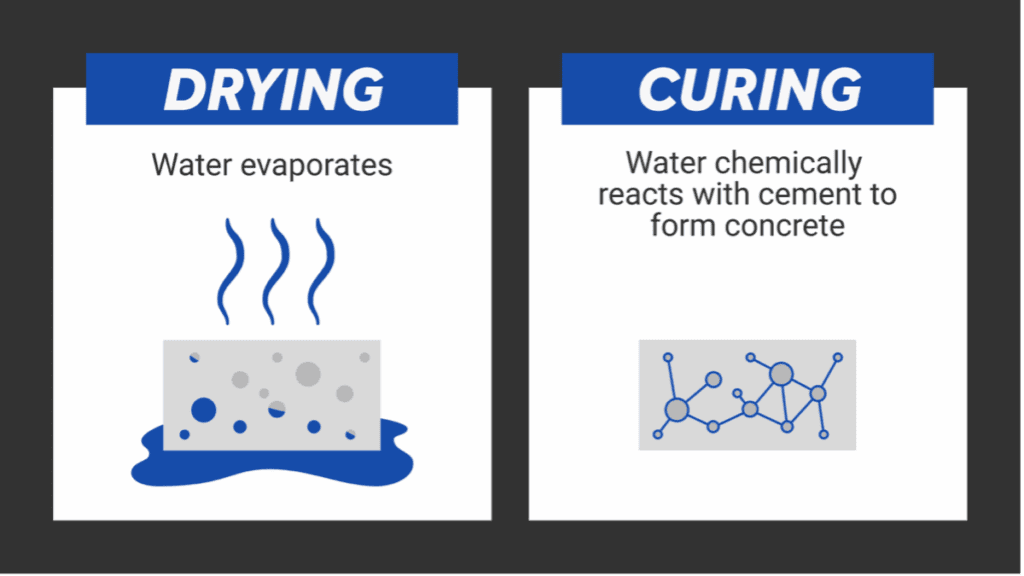
How is Concrete Cured?
Curing is all about keeping concrete moist and within the right temperature range so the hydration process can continue uninterrupted. There are several effective methods, each suited for different job types and environments:
- Wet coverings
Materials like burlap or cotton mats are soaked with water and placed over the surface to retain moisture. - Plastic sheets
These coverings form a barrier to keep water from evaporating. - Curing compounds
Spray-applied products that seal the surface and hold in moisture. - Fogging or misting
Used in high-heat or low-humidity conditions to maintain surface moisture. - Indoor curing
Used in precast and prestressed concrete plants where curing takes place in a controlled environment.
ASTM C511 and C31 standards outline industry-approved practices for maintaining ideal conditions during the curing period.
The Results of Improper vs. Proper Curing
What Happens When Concrete Is Not Cured Properly?
When concrete loses moisture too early, the hydration reaction stops. This leads to:
- Surface cracking due to shrinkage or thermal stress
- Reduced strength, especially in tension zones
- Increased porosity, which allows water and chemicals to penetrate
- Shorter lifespan, requiring more frequent repairs or replacements
Poor curing might not be obvious at first glance, but over time it leads to visible and structural failures.
What Happens When Concrete Is Cured Properly?
With proper curing, the concrete performs as designed. You get:
- Maximum compressive strength for structural support
- Improved durability in harsh weather or chemical environments
- Better bonding with embedded reinforcement and finishes
- Lower maintenance costs over the product’s lifespan
Cured right, concrete can last for generations, especially in critical infrastructure like bridges and industrial buildings.
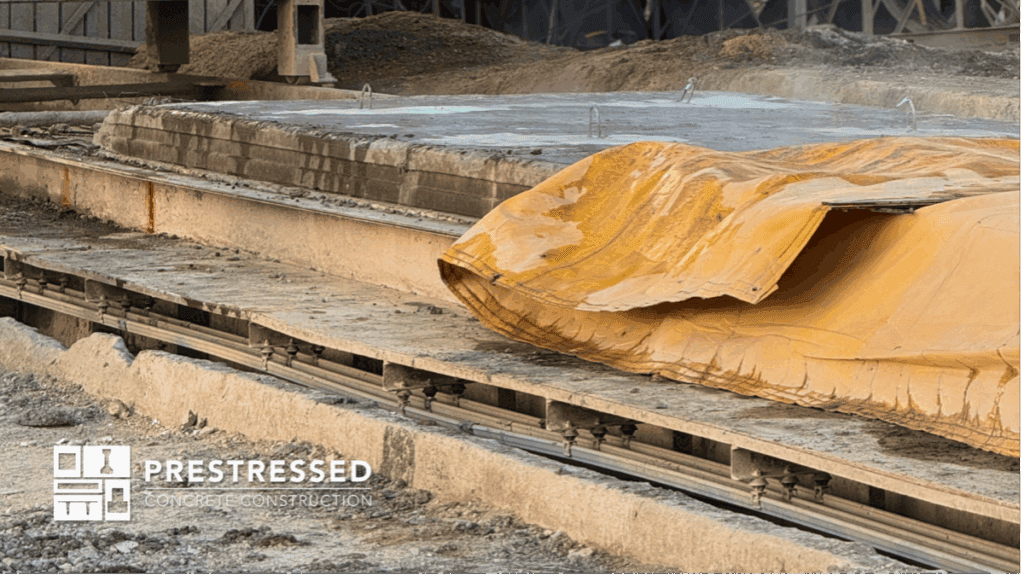
How We Cure Concrete at Prestressed Concrete Construction
At Prestressed Concrete, curing is not an afterthought. It is a built-in part of our production process that ensures every product meets quality and performance expectations before it ever leaves our plant.
Here’s how we do it:
- Controlled environment
Many of our products are made in spaces where temperature and moisture conditions can be consistently managed. - Moisture prevention
We use proven techniques to lock in moisture during early-stage curing. This helps prevent cracking and ensures long-term strength. - Certified strength
Every product is tested before shipment to confirm that it meets the design requirements of your project. You get reliability you can count on.
References
- American Concrete Institute (ACI). ACI 308R-01: Guide to Curing Concrete
- ASTM International. ASTM C31/C31M: Standard Practice for Making and Curing Concrete Test Specimens in the Field
- ASTM C511: Standard Specification for Moist Cabinets, Moist Rooms, and Water Storage Tanks Used in the Testing of Hydraulic Cements and Concretes
- Published in Prestressed Concrete Info
Prestressed Concrete Acquires Stress-Cast
We are thrilled to announce that on August 1, 2024, Prestressed Concrete Construction of Newton, Kansas, acquired Stress-Cast, Inc. of Assaria, Kansas, and its subsidiary, Dynamold. We are excited to welcome the Stress-Cast and Dynamold teams into the Prestressed family. Together, we will continue to build on the integrity and customer service legacy that has made all three companies successful.
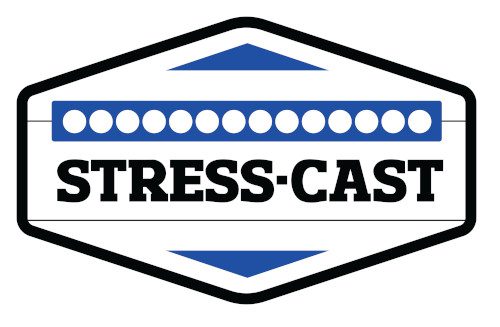
This acquisition is more than a partnership between companies; it’s about helping craft professionals grow their careers and providing quality products to our customers. With this acquisition, Prestressed Concrete Construction will offer more resources, expanded benefits, and boundless opportunities.
Jim Markle, the current President of Stress-Cast, and his team will continue to serve as part of the Prestressed Concrete team. Stress-Cast specializes in producing hollow core concrete, while Dynamold focuses on casting beds, side molds, custom steel machinery, wire mesh for hollow core concrete, and trailers. Stress-Cast has a rich history, starting with Ernest Markle, who took over the business in the late 60s. Jim Markle and his son-in-law represent the third generation involved in the family-run operation. Over the years, Stress-Cast expanded its operations, including acquiring Dynamold in the mid-80s. Both Ernest and Jim have been influential members of the PCI Hollow Core Slab Producers Committee.
If you have any questions about this transition, please feel free to contact me, Brian Curtis, at (620) 202-3770. We are eager to discuss how Prestressed Concrete Construction can continue to serve you with enhanced capabilities and services.
About Prestressed Concrete Construction
Prestressed Concrete Construction offers quality products and personal relationships with endless possibilities. For over 60 years, we have built a strong reputation based on product quality and customer satisfaction across the central US. Our services include in-house design and engineering, drafting, fabrication and production, concrete batching and testing, delivery and installation, and field services. We produce a range of products such as double tees, bridge girders, flat slab wall panels, and double tee wall panels.
We look forward to continuing our partnership and providing you with the high-quality products and services you have come to expect from us.
Stay tuned for more updates and exciting developments! Follow us on our social media channels to keep up with our latest news and innovations. If you have any specific questions or project needs, don’t hesitate to reach out to us directly. We’re here to help you succeed.
- Published in Prestressed Concrete Info
Why Use Prestressed Concrete for Your Parking Garage Project?
Ever drive along the ground level of a parking garage and think about just how much weight is above you?
Ever wonder what’s holding it all up?
Sure there are those giant pillars on the sides and in the middle. But there’s a lot of concrete going on between them with seemingly nothing supporting it.
You can thank prestressed concrete for your safety.
What is prestressed concrete?
Prestressed concrete is, well, exactly that. It’s concrete and steel in which tension was induced long before any weight was put on it. It’s often used in long-spanning projects such as bridges, tall buildings, and parking garages.
Why is prestressed concrete great for parking garages?
Space is a premium in parking garages, and the fewer of those huge beams the better. To ensure there are long spans of parking spots on all levels, using prestressed concrete ensures that the structure is strong and safe enough for the traffic that runs over it every day.
With prestressed concrete, high-strength steel tendons are placed between two abutments and stretched to 70 to 80 percent of their ultimate strength. Concrete is poured into molds around the tendons and allowed to cure.
Applying the initial compression allows the concrete to better handle the external loads that parking garage surfaces face.
Because many parking garages need to be as sleek and/or slender as possible, prestressed concrete is ideal because it has greater shear strength and fatigue resistance.
Before you start your next parking garage project, talk to us about prestressed concrete! You and everyone who uses the garage will be glad you did.
- Published in Prestressed Concrete Info
What Kind of Projects are Prestressed Concrete Slabs Typically Used For?
Using prestressed concrete is a great way of ensuring strength, durability, and longevity of your building project.
But it’s not always necessary. Certain types of projects are better candidates for prestressed concrete than others.
Prestressed concrete is more often used in long-spanning projects with wide open spaces, such as:
- Bridges
- Parking garages
- Tall buildings
- Gymnasiums
- Shopping centers
What do all of these have in common? Long spans of concrete with heavy loads applied every day.
Think about a bridge. Think about how much weight and pressure is put on that long surface every day. Stress, stress, and more stress. If it’s not ready for that, cracks can form and strength becomes an issue.
When you use prestressed concrete to build a bridge, however, it’s better prepared for the pressure because the pretension applied helps improve the concrete’s bendability and structural flexibility.
Prestressed concrete has greater shear strength and fatigue resistance, making it the ideal choice for sleek and/or slender structures that require a large span of wide open space, such as parking garages, shopping centers, gymnasiums, and cafeterias.
Before you start your next project, consider using prestressed concrete as a way of providing strength and stability, all while reducing the risk of cracks!
Interested in using us for your next project? Talk to us about prestressed concrete!
- Published in Prestressed Concrete Info
Prestressed Concrete vs. Reinforced Concrete
Prestressing and reinforcing are two of the main ways of ensuring concrete’s durability and longevity.
And while both provide extra levels of protection and strength, they do so in distinctly different ways.
How does compression work with prestressed concrete?
With prestressed concrete, initial compression is applied to the concrete before ever being exposed to an external load. This initial compression is introduced by high-strength steel wire located in the concrete section.
In prestressing, those steel cables are stretched before the concrete is poured around them. Upon attempting to return to their normal length, the cables become stronger. The end result is concrete with greater tensile strength.
This is why prestressed concrete is often used on long-spanning projects such as bridges, tall buildings, gymnasiums, and parking garages.
What is reinforced concrete used for?
Reinforced concrete is similar in that steel rods, or rebar is inserted into the concrete ahead of the pour. Once the concrete is poured, vibrations are used to remove air pockets and evenly distribute the material.
This process often allows for the customization of shapes and sizes, which is helpful and effective in a variety of architectural projects. Reinforced concrete is often used in columns, foundations, dams, and highways.
Both prestressing and traditional reinforcement are very important to ensure the strength and quality of the concrete. Deciding which concept to use usually depends on the type of project, as prestressing isn’t always necessary.
Before you start your next project, talk to us about your options!
- Published in Prestressed Concrete Info
How to Limit Concrete Cracks with Prestressed Concrete
No matter how much wishing and hoping we do, one unfortunate fact of life is this: concrete cracks. It’s a shame, really.
Cracks are bad for a variety of reasons, such as the threat of moisture seeping in and reduced strength. Plus, it just looks bad. Fortunately, there are ways to limit this pesky truth, and one of the best ways is by prestressing the concrete.
With prestressed concrete, initial compression is applied to the concrete before ever being exposed to an external load. This initial compression is introduced by high-strength steel wire located in the concrete section.
High-strength steel tendons are placed between two abutments and stretched to 70 to 80 percent of their ultimate strength. Concrete is poured into molds around the tendons and allowed to cure.
Applying the initial compression allows the concrete to better handle the external loads, particularly in large, long-spanning projects such as bridges, tall buildings, gymnasiums, and parking garages.
Using prestressed concrete benefits designers and builders, as it allows for lighter and shallower concrete structures without compromising strength.
How Does Prestressed Concrete Work?
Ok, so how does this work? Good question.
Think of a row of books on a bookshelf. If you wanted to move those books all at once, ample pressure needs to be applied to both ends so the books all move together. Once lifted from the bookshelf, the pressure applied before the lift is sufficient to keep the books from falling downward due to gravity.
With concrete, the pretension applied before being subject to external loads helps improve the concrete’s bendability and structural flexibility, which helps avoid cracks.
Prestressed concrete has greater shear strength and fatigue resistance, making it the ideal choice for sleek and/or slender structures.
Need More Info? Contact Us!
Before you start your next project, consider using prestressed concrete as a way of providing strength and stability, all while reducing the risk of cracks! Contact us today to learn more or discuss your project.
- Published in Prestressed Concrete Info