Precast vs. Cast-in-Place Concrete: Which One is Right for Your Project?
When planning a construction project, choosing the right concrete method is critical for ensuring efficiency, cost-effectiveness, and long-term durability. Two of the most common methods used in modern construction are precast concrete and cast-in-place concrete.
Each has distinct advantages and disadvantages depending on your project’s specific requirements, timeline, and budget. Let’s compare the two to help you determine which method is the best fit for your next build.
What is Precast Concrete?
Precast concrete is manufactured off-site in a controlled environment, where it is cast into forms, cured, finished, and then transported to the construction site for installation. At Prestressed Concrete Construction, to assure quality we have control over each step of the process – from mixing our own high-strength concrete, to cutting and fabricating steel reinforcements and embeds, to using prestressing strand for added strength. Precast concrete is commonly used in bridges, storm shelters, parking structures, and more.
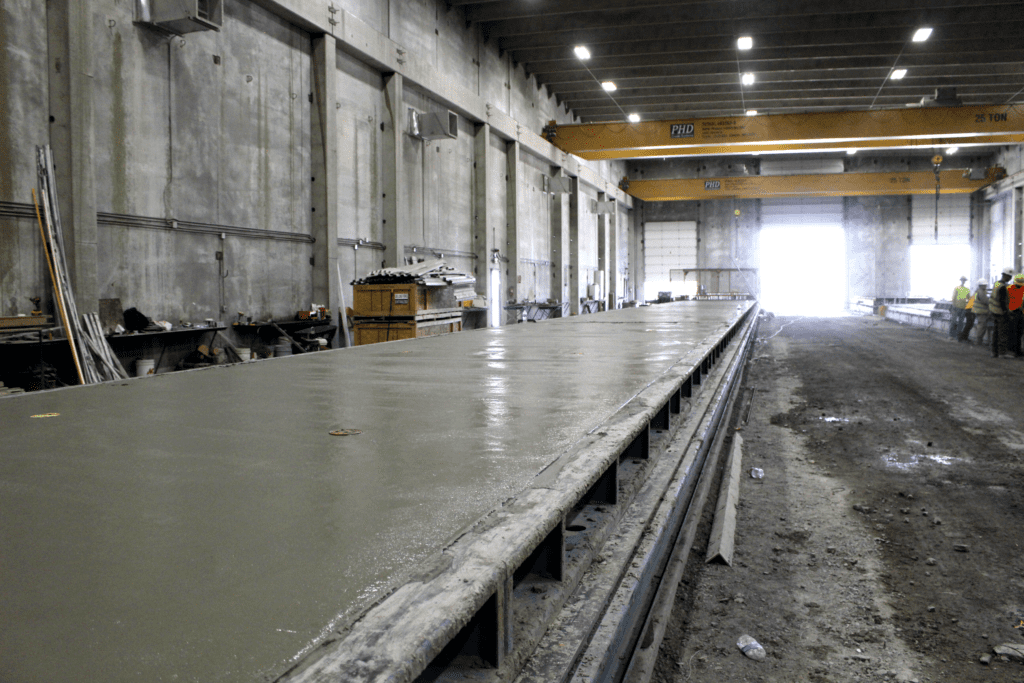
Advantages of Precast Concrete
- Faster Construction Timelines
Since precast concrete is produced off-site, site work and production can happen simultaneously—speeding up the overall construction timeline. - Higher Quality Control
Prestressed Concrete Construction’s Newton facility features an indoor production environment, allowing for precise quality control and minimizing defects caused by weather or temperature fluctuations. - Durability & Strength
Precast concrete is highly resistant to environmental stressors, including extreme temperatures and moisture. That’s why it’s a top choice for structures like storm shelters. - Reduced On-Site Labor
With components arriving ready for assembly, less on-site labor is required—enhancing safety and reducing labor costs. - Lower Long-Term Maintenance
Controlled curing leads to fewer cracks and inconsistencies, which means lower maintenance needs over time.
Disadvantages of Precast Concrete
- High Initial Transportation Costs
Transporting large precast elements from the facility to the job site can add to upfront project costs. - Limited Flexibility for Changes
Once components are cast, design changes can be difficult and costly to implement. - Heavy Equipment Required for Installation
Installing large precast pieces often requires cranes or other specialized machinery, which may not suit every job site.
What is Cast-in-Place Concrete?
Cast-in-place (or site-cast) concrete is poured, molded, and cured directly at the construction site. It is commonly used for foundations, slabs, roads, and other large commercial structures.
Advantages of Cast-in-Place Concrete
- More Design Flexibility
Because the concrete is poured on-site, contractors can make last-minute adjustments more easily. - Lower Transportation Costs
No need to transport pre-made elements—materials are mixed and poured on location. - Stronger Monolithic Structures
On-site pouring creates continuous, seamless structures with fewer joints and weak points. - No Heavy Lifting Equipment Required
This method eliminates the need for cranes or hoisting machinery, simplifying logistics on the job site.
Disadvantages of Cast-in-Place Concrete
- Longer Construction Timelines
On-site pouring and curing take time, often leading to slower project completion. - Weather Dependent
Curing is sensitive to rain, extreme temperatures, and humidity, which can lead to delays or compromised quality. - Higher Labor Costs
Formwork, pouring, and finishing require more labor on-site, increasing labor-related expenses. - Inconsistent Quality
Site conditions vary, making it harder to achieve the consistency and precision of factory-cast components.
Which One is Right for Your Project?
Choose Precast Concrete If:
- You need faster timelines and minimal on-site labor
- Quality and consistency are top priorities
- Weather conditions at your site are unpredictable
- You’re working with modular elements like beams or panels
Choose Cast-in-Place Concrete If:
- Transporting large components is cost-prohibitive
- A continuous slab or monolithic structure is required
- Your schedule allows for extended on-site curing
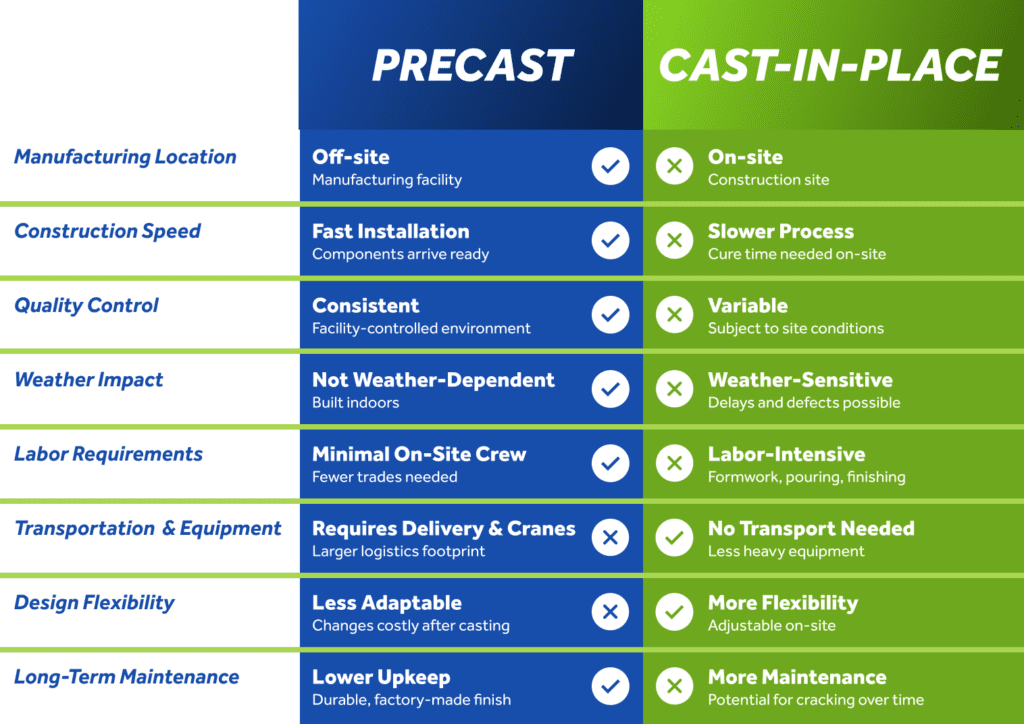
Final Thoughts
Both precast and cast-in-place concrete have unique advantages. The best option depends on your project’s scope, goals, and constraints.
At Prestressed Concrete Construction, we specialize in delivering high-performance precast solutions that save time and improve long-term durability. If you’re exploring precast or prestressed options, we’re here to help.
- Published in Uncategorized
Precast Concrete Joins the Productions Lineup
Rob Newsom is leading PCC’s precast concrete team to new heights. His ability to streamline production brings high levels of efficiency to our precast division. With the implementation of Lean Construction practices, we are able to offer precast building components that exceed project owner expectations. “Rob is a champion for safety and continuous improvement. Not only does his motivation drive his own efforts, it inspires his team to get better every day, said Chris Goevert, General Manager. “Whether it’s with education materials or with his can-do attitude, Rob truly elevates this part of our business. His skills and expertise are second to none. If it’s precast concrete, you can trust that his team will deliver.”
- Published in Uncategorized
Prestressed Concrete Company, Inc announces new General Plant Manager, Chris Goevert.
Prestressed Concrete Company welcomes Chris Goevert, General Plant Manager, to our team. With more than 27 years of experience in the commercial construction industry, Chris is a skilled leader with an unsurpassed knowledge of field practices and project management. “Joining the Prestressed team at this point in my career is a real-life example of ‘right place, right time.’ I am blessed to work with these dedicated employees whose cumulative goals and determination push the envelope of excellence beyond expectation. This company has enjoyed 60 years of success – together, we will continue to build that legacy.” – Chris Goevert
- Published in Uncategorized
Newton, Kansas concrete company debuts industry-sought 12 foot double tees
Prestressed Concrete Construction, located in Newton, Kansas, announces their product-line expansion to include double tees with panels measuring 12 feet in width, each individually prestressed up to 650,000 pounds (650 Kips). Poured locally, the new 12 foot double tee panels will have a 30-inch leg depth with a minimum 2 inch deck; additional product specifications include the prestressing of each 12 foot panel leg. The new equipment provides PCC with the capacity to better serve prospective warehouse and parking garage project owners. The plant expansion also includes upgrades to all onsite concrete batch plants and additions to their panel placement equipment fleet.
“We are excited to offer our customers the 12 foot wide panel. Previous panel pours were limited to 8 foot panel sections. From a value standpoint, the 12 footers will reduce the piece count of their product orders, which, in turn, reduces both the number of jobsite panel delivery trips and the number of pieces required to install and complete the project. It’s a move that will decrease overall consumer cost, and provides an option that has been largely otherwise unavailable. PCC has always been known for superior products. The plant additions and improvements just up our game that much more,” said General Manager, Chris Goevert. Production is slated for December 2017.
- Published in Uncategorized